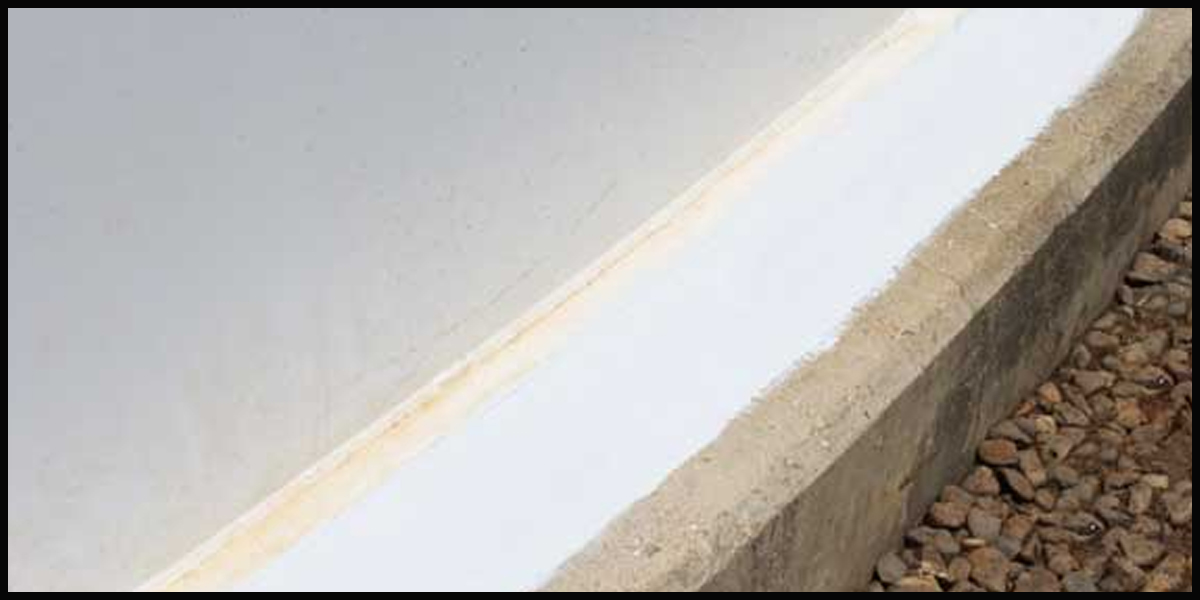
IVYS Chime Coating: Protecting Storage Facilities
IVYS takes pride in its leadership in Chime Coating for bulk storage tanks within the oil and gas industries. Our specialized coating solutions safeguard critical tank components such as the annular plate, shell bottom seam, and ring wall from corrosion, ultraviolet radiation, and water seepage.
Best Chime Coating Services
We offer the best Chime Coating services for unbeatable protection and stunning looks. We specialize in enhancing durability and beauty, shielding surfaces from wear and corrosion. Our expert application ensures lasting quality and a flawless finish. Trust us to deliver superior Chime Coating solutions tailored to your needs.
Challenges in Tank Chime Protection
Tank chimes are particularly vulnerable to corrosion due to factors like condensation, corrosive dew formation, and exposure to atmospheric compounds such as carbonic and sulfuric acids. This environment can lead to heavy pitting, pinhole development, and larger holes, compromising the structural integrity of the tank. Vapor loss and water seepage not only lead to product contamination but also accelerate internal corrosion.
IVYS Chime Coating Methodology
IVYS employs a specially formulated anti-rust, water, and weatherproof coating known as Barrier TCP. This coating is designed to adhere strongly to metallic surfaces such as steel, GI steel, and stainless steel, offering up to 300% elongation to accommodate substrate movement and preventing atmospheric corrosion.
Application Process
Before applying Barrier TCP, the tank surface undergoes rigorous cleaning through power tool cleaning ST3 (SSPC-SP3) to remove contaminants. An initial anti-rust coat prepares the surface for optimal adhesion. Any existing holes are patched using barrier fabric, followed by the application of the Barrier TCP coating. The coating process involves laying fabric tissue and applying subsequent coats with intervals of 4-6 hours, depending on atmospheric conditions.
Suitable Applications
Barrier TCP is ideal for hydrocarbon storage tanks containing fuels like kerosene, jet fuel, LPG, diesel, petrol, and crude oil. Its robust protective properties ensure long-term resistance against corrosive elements, enhancing the longevity and reliability of storage tanks in demanding industrial environments.